Topics
Cathodic arc deposition
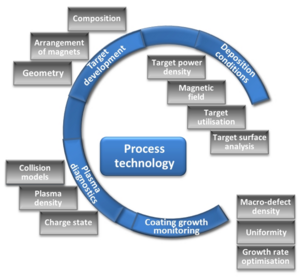
Cathodic arc evaporation is a specific PVD technique relying on evaporation of the cathode material under high-current low-voltage conditions. During cathodic arc evaporation the cathode surface material is rapidly transformed from a solid to plasma state by a combination of intense ion bombardment and ohmic heating. The condensation of the high-energy flux of gas and cathode ions on a sample surface enables formation of coatings with very high density and possibly metastable structures.
Cathodic arc deposition is used for growing single or multilayer structures of different materials, forming a hard film to protect the surface of the base material.
Coating development
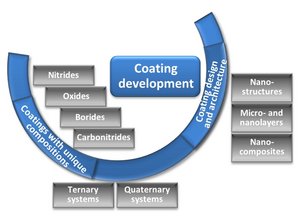
The main goal is the development of materials with unique compositions, microstructure, architecture and properties. The activities within this task are focused on the development of new materials, optimisation of their microstructure, stress state, mechanical and thermal properties as well as other functional properties required for specific applications (e.g. low friction, high thermal stability, high wear and oxidation resistance).
Advanced analytical methodes
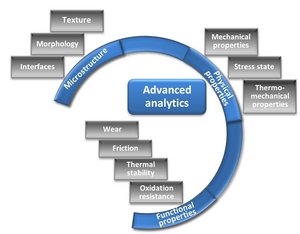
Advanced analytical methodes
Advanced analytics” is thus dedicated to determination of microstructure and physical and functional properties of coatings synthesized within process technology and coating development by a combination of micro- and macro- ex-situ and in-situ material characterization methods. The main focus of the activities will be concerned to establish multi-scale relations between the coating microstructure in terms of texture, morphology and interfaces and the physical and functional properties such as hardness, elastic properties, fracture toughness, stress state, wear and friction.
Application-relevant testing
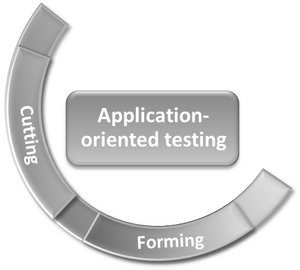
Application-relevant testing
The performance of the developed coatings in high-speed cutting and hot-forming applications cannot easily be determined without application-relevant test methods including high operation temperatures and high forces applied locally in the contact zone. High-speed cutting and high performance cutting tests will thus be performed by the project partners to study coating characteristics under real conditions.